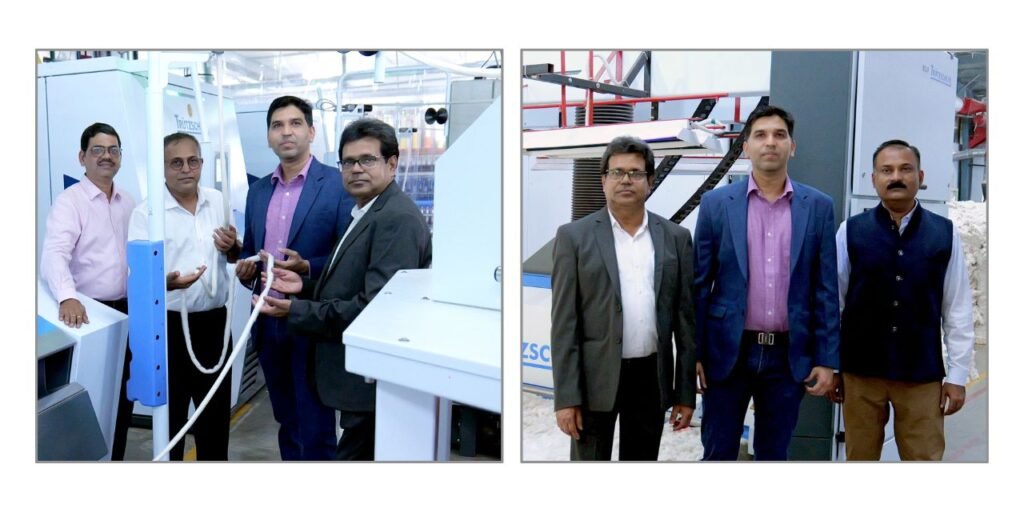
Vineet Mohota (Director Gimatex), Gautam Kumar Dhang (CEO Fabric Business Gimatex), Shailesh Thakur (Deputy General Manager Sales ATE), and Shiladitya Joshi (Deputy General Manager Marketing Trützschler) are seen from left to right. Gautam Kumar Dhang (CEO, Fabric Business Gimatex), from left to right Gimatex Director Vineet Mohota and General Manager Gimatex Manish Deolankar in front of the Bale Opener Trützschler.
Trützschler and Gimatex, an Indian corporation, have been associated since 2006. They have since worked well together on other projects. Trützschler’s IDF has been effectively applied in direct spinning by Gimatex. They are now utilizing it to create valuable ring yarn out of textile waste.
Gimatex Industries Pvt. Ltd. holds sustainability and quality to very high standards. Within Vidarbha, India’s principal cotton-growing area, the firm has fully integrated facilities including ginning, spinning, recycling, weaving, and processing plants in Hinganghat. Additionally, it operates a cutting-edge fabric processing facility in Near Ahmedabad is Dholka. It has a lot in common with being a family-owned business with over 125 years of existence. in conjunction with Trützschler. The two parties are cooperating closely together with the common goal of stretching far into the future that lengthy history.
“Our customers expect reliable quality and affordable costs,” says Gimatex Director Mr. Vineet Mohota. “We always use the newest technology to improve quality, conserve energy, and advance sustainability in order to satisfy those needs. Trützschler is a reliable collaborator on the project.
Increased productivity and decreased expenses
The core of this partnership is the Integrated Draw Frame (IDF) technology from Trützschler. Gimatex is producing high-quality yarn by utilizing these creative methods. Specifically, Gimatex can create premium yarns from an exceptionally broad range of raw materials thanks to IDF, including polyester, 100 percent cotton, and repurposed materials and mixtures of diverse sources.
Gimatex mostly employs Trützschler IDF in a direct spinning process to produce rotor yarns. By removing draw frame segments, direct spinning reduces the spinning time. Slivers of fiber are supplied into the integrated drafting route straight from the card. This direct spinning concept uses less electricity and less space than conventional draw frame passages, which helps Gimatex to cut costs while increasing output volumes – with no compromise in quality. Most often, IDF technology is used for rotor and vortex spinning. .. To make both traditional and recycled ring yarn, the Gimatex team is currently among the first spinning mills in India to create a unique IDF technique. This enables the business to utilize the same configuration that it employs for open-end yarn. This unconventional method produces ring yarn that is often coarser. varieties and recycling mixes with Ne 10s and Ne 16s for goods made of cotton and spandex (lycra). The yarn moves via a blow room, into an IDF-equipped TC 15 card, and then into a Trützschler TD 10 draw frame, a rapid a ring frame and a frame
enduring collaboration
Mr. Mohota states, “The performance of Trützschler’s IDF machines is great.” The knowledgeable experts at Trützschler also assist us. They’re always available to give guidance and answer questions, and they’re able to access data from around the globe to share best practices for every application.” Gimatex and Trützschler have established a close relationship over a long period. IDF machines are a flexible, highly efficient and sustainable technology that is helping to extend that valuable partnership. As market conditions in India continue to evolve, we will keep working hand in hand to adapt to change successfully – while meeting high expectations from customers.
About the Group Trützschler:
Based in Münchengladbach, Germany, the Trützschler Group SE is a manufacturer of textile machinery. Three business units comprise the company: Spinning, Nonwovens, and Card Clothes. Trützschler equipment, installations, and spare parts are created and manufactured in nine places all across the world. Among these are four German manufacturers (Dülmen, Egelsbach, Mönchengladbach, Neubulach), in addition to locations in the United States (Charlotte), China (Jiaxing and Shanghai), India (Ahmedabad), and Brazil, specifically Curitiba. Local service providers and businesses in Turkey, Mexico, Uzbekistan, and Vietnam Teams in Bangladesh, Indonesia, and Pakistan offer close client closeness in strategic textile regions. processing sector. To learn more, go to www.truetzschler.com.