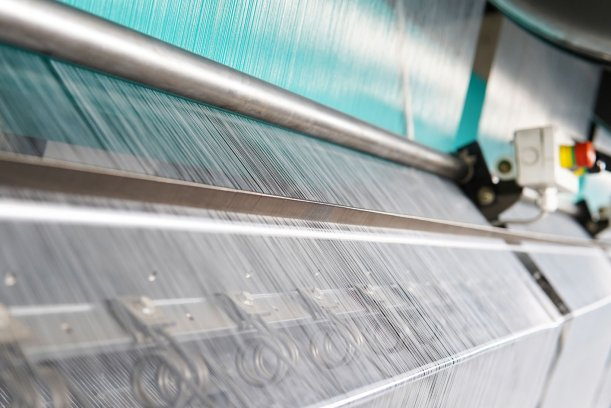
Sidestepping complex processes and considerable trial-and-error loops.
The new Energy Efficiency Solution for warp knitting machines from Karl Mayer is a cloud-based solution that combines the latest sensor technology with a specifically-developed analysis software.
“Energy efficiency is becoming increasingly important for production companies, due to rising energy costs, stricter environmental regulations and a growing awareness of environmental concerns, particularly in the machinery sector,” says Karl Mayer digital product owner Markus Bahde. “Through active and continuous management, huge savings in costs and CO2 emissions are possible,”
Continuously recording and analysing data on real consumption enables companies to manage energy efficiently, he adds, but may require a significant amount of measurement technology, personnel and time. In addition, there are currently only a few experts with real-world experience in energy issues from the field of production. As a result the implementation of energy data analysis often involves complex processes with considerable trial-and-error loops.
With its new Energy Efficiency Solution, Karl Mayer is taking a simpler and more efficient path by enabling machine users to visualise selected data to identify their energy consumption, by displaysingthe captured and processed data of networked machines and recording the power consumption for production, heating and standby operation modes.
Companies wishing to leverage these opportunities will have easy access to the solution via my.KM.ON, the Karl Mayer customer portal.
They can gain an overview of their production processes by displaying the energy data of individual machines and the entire machine fleet in real time, for example, generating an energy data analysis from the past and using it fir their own energy reports. In addition, it is possible to efficiently control machine heat-up without manual configuration on site.
An overview of the current consumption data with a graduated viewing depth is another benefit and for more dedicated monitoring, the values for the current day, week, month and year can be output.
A closer look reveals more details. The display also contains the details of the performance and energy data of an individual machine, broken down according to machine status and parameters for the power supply.